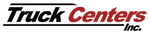
ComplaintsforTruck Centers Inc
Need to file a complaint?
BBB is here to help. We'll guide you through the process.
Complaint Details
Note that complaint text that is displayed might not represent all complaints filed with BBB. See details.
Initial Complaint
04/26/2024
- Complaint Type:
- Service or Repair Issues
- Status:
- Answered
On 4/16/2024, I went to the Truck Centers located at ****************************************************************************** to get an issue fixed with my semi rig truck to get an inlet sensor replaced. After waiting for approximately 3 hours for services. *************************, the service advisor came back and acknowledge there was an issue that the mechanic removed a fairing disconnected sensor to re probe however the sensor was frozen, the mechanic heated the sensor, and the mechanic also broke the sensor probe off in the bung. The shop ******* advised the service advisor of the situation that he had made the error of putting heat to a frozen part that did not require applying heat at all!! ******, the service advisor had recently given me a quote for $2420.56 from the start. Then later came back and stated there would be an increase from $2420.56 to $3700. I disagreed with the fact amount the increase amount for the fact that they broke the part but wanted me to pay for the increase amount that their mechanic damaged and broke the part and never took responsibility for the sensor that he broke, the inlet sensor was not broke before I entered the premises. Then they threaten to call the police on me if I didn't leave immediately. Therefore, I am requesting a refund of $742.71 plus the part that they broke for $418.17 plus the labor they were charging that totaled $3700 plus the load that I was delivering for $5500 by promising me that they would have me back on the road in as little as 3 hours.Business response
05/20/2024
Good afternoon,
My name is ***************************, and I am the General Manager at Truck Centers, **** in St. Louis. I am responding to ********************** complaint regarding a damaged part due to the heating of a rusted and frozen NOx Sensor.
****************** arrived and was attended to on April 15, 2024, with a request to "Check and advise on both orange check engine lights being on and the unit being de-rated to 55 mph." Upon troubleshooting, it was determined that the inlet NOx Sensor needed to be replaced. The technician also noted a coolant leak around the surge tank/radiator area.
The technician found that the NOx Sensor was rusted and frozen in place. Since these sensors are part of the exhaust system, they tend to rust and become difficult to remove. The standard procedure involves heating the bung that the sensor screws into using a torch, which helps in removing the sensor. This is a common practice not only for Class 8 trucks, but also for cars.
Here's why heating is an effective technique for freeing rusted and frozen parts:
1. Thermal Expansion: When metals are heated, they expand. By heating a rusted or frozen part, a mechanic can cause the metal to expand. This can break the bond created by rust and help loosen the part. The expansion is usually uneven, which can help break the grip that rust has on parts.
2. Breaking Rust Bonds: Rust forms a strong bond between metal parts, making them difficult to move. When heat is applied, it can change the physical properties of the rust, making it more brittle and easier to break apart.
3. Differential Expansion: Different metals expand at different rates. If the part being heated is made of a different metal than the part it's stuck to,the differing expansion rates can help to break the rust bond.
4. Lubrication: In conjunction with heating, mechanics often use penetrating oils. Heating the parts can enhance the penetration of lubricants, as the heat can thin the oil, allowing it to seep into tighter spaces more easily.
5. Stress Relief: Heating the metal can relieve some of the residual stresses within the material, which can ease the movement of the stuck parts.
6. Material Properties: Heat can also make certain metal alloys more malleable and less brittle, making it easier to manipulate the parts without breaking them.
7. Corrosion Control: Heat can help in the reduction of certain types of corrosion or help initiate chemical reactions that assist in breaking down rust layers.
It's important to note that parts sometimes break despite our best efforts, and this cannot always be prevented. The method described above is a standard procedure and is also used in warranty situations, where if a part breaks, it becomes part of the warranty claim. This is not the fault of the technician. This procedure and its risks were explained to ******************, and he was provided with a quote to repair the unit correctly. However, ****************** refused the repair and chose to take the unit as it was.Our technician adhered to standard procedures, and we believe that ********************** complaint should therefore be withdrawn.Thank you for your assistance in this matter.Sincerely,
Sincerely,
***************************
General Manager
Truck Centers, ****
************
**************************************
Initial Complaint
11/05/2022
- Complaint Type:
- Service or Repair Issues
- Status:
- Answered
on 10/20/22 truck centers told me I had to buy an oil pan n handed me an estimate for $3600 for a stripped oil plug. truck centers were the only ones who done my oil changes for 3 years. how was that my fault I was told on 2 separate occasions a resolution that the manager conveniently said I miss understood him. I missed 2 weeks of work because of this then on the receipt they put my oil change but under the oil pan they put miscellaneous so in the future there's no liability on what they break! the truck centers on ****** *** is unreliable on their work ethic as proven to me in the past.Business response
11/21/2022
Truck Centers Inc of St. Louis notified Mr. ******* verbally and in writing that he had wear to the drain plug / oil pan threads on his previous preventative maintenance service (********** 8/17/2022). The drain plug is a removable item and therefore subject to wear. This particular part has over 1.5 million miles of use, and assuming the recommended oil change interval of 25,000 miles is followed, has been removed over 60 times during operation. Mr. ******* also had repairs made, by a different repair shop, to another drain plug on this unit using unapproved repair techniques in close proximity to the plug in question. Unqualified personnel welding cast aluminum in close proximity to this drain plug will cause expansion and contraction to occur which could cause this joint to fail. (pictures of welded drain plug attached)
Mr. ******* brought his unit in on 10/08/2022 for another preventative maintenance service (**********) and was again informed of the damaged threads on the oil pan. Given the repair history to the oil pan it was our recommendation to replace the pan with a new unit. Mr. ******* was concerned with the cost of a new unit and we discussed other options like installing a good used part if one could be found. Mr. ******* expressed an interest in the used part option, had a vendor that he wanted to use (*** ***** ****** ** ******* ***** **), and was informed to update us once he found a suitable replacement. Mr. ******* notified us that his vendor found an oil pan and requested that we inspect it for use. The service manager of TCI St. Louis drove over to *** ***** ****** to inspect the item, at no charge to the customer, and found that the pan was wrong for the application. The vendor had another oil pan, but would need to remove it from the vehicle it was currently installed on. On 10/12/22 Mr. ******* was informed to notify us once his vendor had removed the oil pan. On 10/14/22 Mr. ******* was informed, again, that we were awaiting word from him on his vendors used oil pan. Between 10/15/22 and 10/17/22 discussions were had between Mr. ******* and the general manager to share the cost of a new pan replacement as a sign of good will due to the delay in a used part option (not caused by TCI).
On 10/18/22 the new oil pan was installed, the preventative maintenance service was performed, which Mr. ******* originally requested, the invoice settled, and the unit released back to the customer. Truck Centers Inc goodwilled $1,014.09 in parts and labor on this repair (**********-2).
The above statement is fact backed up by documentation, below are my thoughts:
No other vendor in the area would have went to the lengths that *** went to in an attempt to make things right given the situation with this customer.
Initial Complaint
08/02/2022
- Complaint Type:
- Service or Repair Issues
- Status:
- Answered
Took my truck in to the dealership for a low oil pressure. They charge me a lot of money and when I left and got back on the road some ways out My truck started to have the same problems. Had to take it to another Freightliner dealership in Kansas City Missouri. At that time they informed me that they did not do a diagnostics on the truck there and asked me why did they take my truck apart. Said that the only thing that they found was wrong with my truck because they had to do a diagnostic test on it was that I had a bad oil sensor. I lost my load that week because of their mistake.Business response
08/02/2022
Good evening. We need to ask for the customer to share the Company Name with Truck Number or the last 6 of the Vin or the Invoice number. We need more information unfortunately than what this complaint has for details. We don’t have anything in our system under just her name. We will work to resolve it ASAP if we can get that information.
Thank you for the help.
*Some consumers may elect to not publish the details of their complaints, some complaints may not meet BBB's standards for publication, or BBB may display a portion of complaints when a high volume is received for a particular business. ↩
BBB Business Profiles may not be reproduced for sales or promotional purposes.
BBB Business Profiles are provided solely to assist you in exercising your own best judgment. BBB asks third parties who publish complaints, reviews and/or responses on this website to affirm that the information provided is accurate. However, BBB does not verify the accuracy of information provided by third parties, and does not guarantee the accuracy of any information in Business Profiles.
When considering complaint information, please take into account the company's size and volume of transactions, and understand that the nature of complaints and a firm's responses to them are often more important than the number of complaints.
BBB Business Profiles generally cover a three-year reporting period. BBB Business Profiles are subject to change at any time. If you choose to do business with this business, please let the business know that you contacted BBB for a BBB Business Profile.
As a matter of policy, BBB does not endorse any product, service or business. Businesses are under no obligation to seek BBB accreditation, and some businesses are not accredited because they have not sought BBB accreditation.
Customer Reviews are not used in the calculation of BBB Rating
Contact Information
2280 Formosa Rd
Troy, IL 62294-3170
Business hours
Today,6:00 AM - 12:00 AM
MMonday | 6:00 AM - 12:00 AM |
---|---|
TTuesday | 6:00 AM - 12:00 AM |
WWednesday | 6:00 AM - 12:00 AM |
ThThursday | 6:00 AM - 12:00 AM |
FFriday | 6:00 AM - 12:00 AM |
SaSaturday | 6:00 AM - 6:00 PM |
SuSunday | 6:00 AM - 6:00 PM |
Want a quote from this business?
Get a QuoteCustomer Complaints Summary
3 total complaints in the last 3 years.
1 complaints closed in the last 12 months.